Safety
Why are liquefied cargoes a persistent danger to ships?
Solid bulk cargoes – defined as granular materials loaded directly into a ship’s hold – can suddenly turn from a solid state into a liquid state in a process known as liquefaction. IMO guidelines exist to instruct shippers on how to avoid the potential dangers, so why does liquefaction remain such a menace? Patrick Kingsland reports
Image courtesy of
At roughly 7am
on 2 January 2015, the Bulk Jupiter– a supramax bulk carrier built in 2006 – foundered in the South China Sea, roughly 150 miles off the coast of Vietnam. Of the 19 crew members on board just one, a chief cook, managed to survive after eight hours in the water.
The cause of the sinking was not a collision, a freak storm or a problem caused by dangerous cargo - but a strange, sadly all-to-common phenomenon that is little understood by the general public: cargo liquefaction.
The phenomenon is triggered by an increase in water pressure that makes solid bulk cargoes (granular materials that are loaded directly into a ship’s hold) turn from a solid state into a liquid state, causing a ship to tilt and potentially capsize. It can occur when cargo is loaded into the hold - this often involves a fall from significant heights, or when it is exposed to agitation by the ship’s engine vibration or movement of the waves.
Stuart Rivers, CEO of Sailors’ Society.
Image courtesy of Sailors’ Society
Cargo liquefaction: a string of incidents
The Bulk Jupiter, which was carrying 46,400 tonnes of bauxite when it foundered, was just one of a string of recent incidents involving cargo liquefaction.
In 2013, 15 people died after the Panama-registered Harita Bauxite vessel, which was carrying nickel ore, sunk in just 30 minutes off Cape Bolinao in the South China Sea.
Two years earlier, 21 crew members on board the Vinalines Queen lost their lives when the ship sunk en route from Indonesia to China. It had 54,000 tonnes of nickel ore in its hold.
“When you have cargo liquefaction, generally you lose the vessel and the loss of life is significant,” says Susan Gourvenec, professor of offshore geotechnical engineering at the University of Southampton. “Other types of vessel loss or incidents don't have such a high fatality rate.”
When you have cargo liquefaction, the loss of life is significant
According to Gourvenec, the number of accidents has increased as a wider variety of cargo is transported often in new, emerging markets that are less equipped to manage the risks.
A company shipping iron ore from a big industrial port in a dry climate like north-western Australia might not face any problems for example, but in a wet climate such as the Philippines, where loading procedures for finer grade materials are not standardised, the risks can be much higher.
“There are a lot of economic pressures in the industry and some of the new players in the sector are developing countries which lack the investment and infrastructure that may historically have been more accepted,” says Gourvenec.
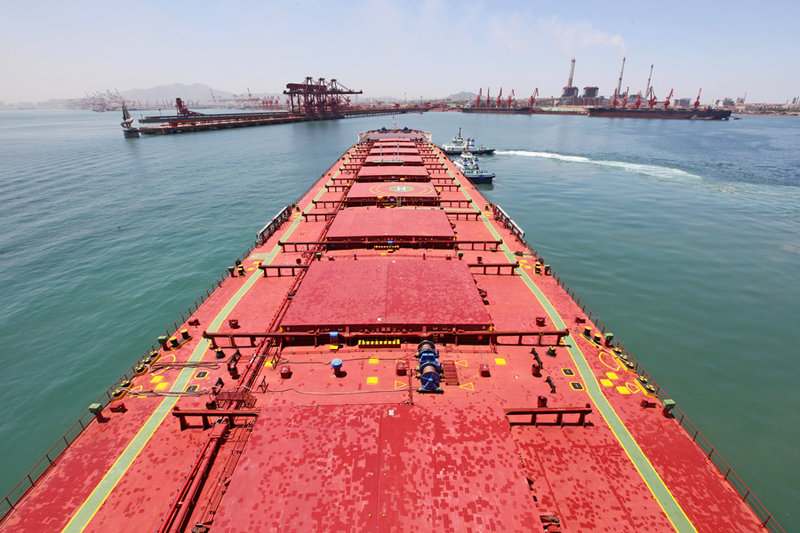
Image courtesy of
Image courtesy of
Risk reduction: action on liquefaction
Awareness of the risk of cargo liquefaction has certainly improved over the years. Following a string of iron ore incidents, an iron ore working group was set up through the International Maritime Organization (IMO). After a number of problems involving bauxite, a similar working group was also created for that commodity.
In January 2011, the International Maritime Solid Bulk Cargoes Code (IMSBC) became mandatory, replacing the Code of Safe Practice for Solid Bulk Cargoes, which was first introduced in 1965. The new code provided information on the characteristics of different cargoes and instructions on how solid bulk cargoes should be carried.
But despite these efforts, bulk carriers continue to sink. Analysts say the IMO code is not always applied and that the measures in place to test cargoes for liquefaction are inadequate.
We need to have a more robust way of naming cargoes and certifying them for transport
“They are not comprehensive enough to identify all of the potentially dangerous cargoes,” says Gourvenec. “They are too simplistic and don't measure enough characteristics of the material to be able to judge liquefaction potential.”
Given the greater variety of cargoes being shipped, Gourvenec says the solution is to have a better understanding of the materials that are used in the industry and then implement a more appropriate, rigorous testing regime.
“We need to have a more robust way of naming [cargoes] and certifying them for transport,” she says. “Then we need to prescribe appropriate testing for the materials and potentially geographically relevant testing protocols that consider the climate of the country or origin of the material, or the socio-economic conditions.”
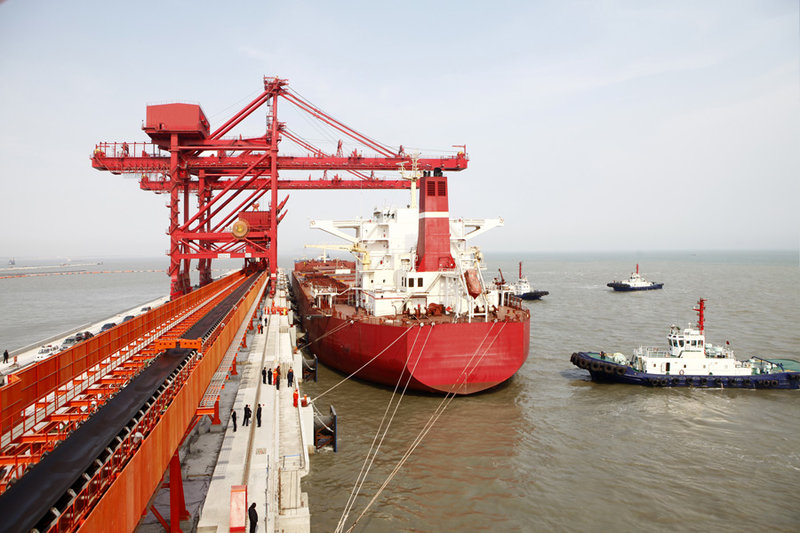
Image courtesy of
Tech solutions
The advent of new technology in the shipping industry could help reduce the risks going forward. Gourvenec says sensors could be used to monitor the water pressure of the cargo while it is in the hold, for example. This could be coupled with smart weather forecasting software which detects how using different routes could cause pressure in the cargo to rise.
Producing such a technology isn’t easy, however. It must be cheap, easy to install, robust enough to withstand loading and unloading, and needs to work in a number of different settings.
There are various pathways to a solution
“It is a very bespoke challenge,” Gourvenec says. “The weather is always going to be very different and the cargo varies tremendously: the same vessel may carry all sorts of different materials depending on the voyage it is on.”
But Gourvenec remains optimistic a solution can be found: “There are various pathways to a solution,” she says. “You could retrofit existing vessels with the technology, or with a better understanding of the challenges, bring new vessels into the industry that are capable of doing it.”